إزالة الكريون من عملياتنا
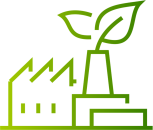
إزالة الكريون من عملياتنا
طريقنا نحو تحييد الكربون
لقد بدأ برنامج "المستقبل يبدأ الان" في عملياتنا، فنحن نطور عمليات الانتاج لدينا في كل خطوة من خطوات العمل.
ويركز برنامج " المستقبل يبدأ الان" على التوسع في اربعة مستوبات تهدف غلى تقليل انبعاثات الكربون وتحقيق اهداف ٢٠٣٠، ألا وهي:
- زيادة استخدام الوقود البديل عوضًا عن الوقود الاحفوري المعتاد.
- تقليل عامل الكلنكر في الاسمنت لدينا
- تحسين الكفاءة الحرارية في افراننا
- استخدام المواد الخام منزوعة الكربون
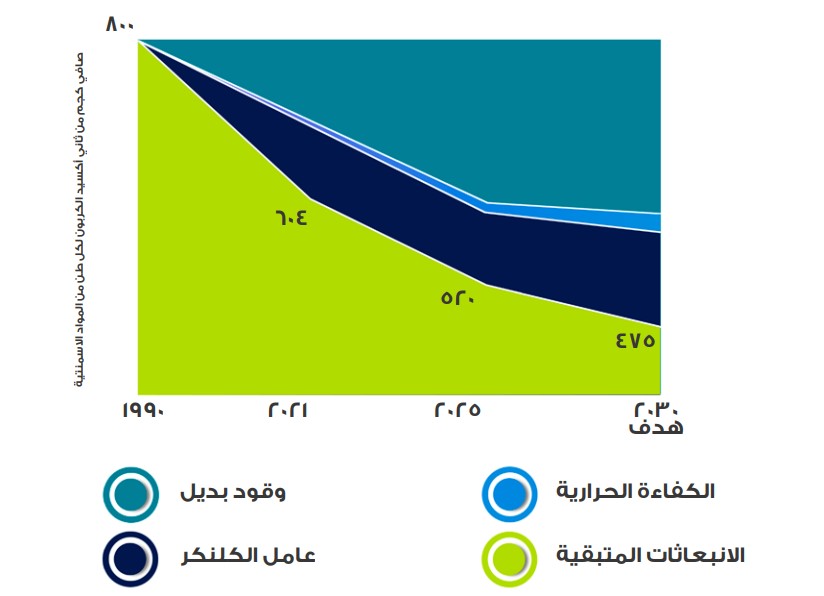
ويركز برنامج " المستقبل يبدأ الان" على التوسع في اربعة مستوبات تهدف غلى تقليل انبعاثات الكربون وتحقيق اهداف ٢٠٣٠، ألا وهي:
- زيادة استخدام الوقود البديل عوضًا عن الوقود الاحفوري المعتاد.
- تقليل عامل الكلنكر في الاسمنت لدينا
- تحسين الكفاءة الحرارية في افراننا
- استخدام المواد الخام منزوعة الكربون
الوقود البديل واستخدام النفايات في عملية التصنيع
يمكن للوقود البديل القضاء على عملية الاعتماد لدينا على الوقود الاحفوري، كما يمكنه تشغيل الافران لدينا مع توفير مزايا أخرى لخدمة البيئة؛ فالوقود البديل، وبوجه خاص الكتلة الحيوية، هو عبارة عن منتج بشري ثانوي ينتهي به الامر إلى مدافن النفايات، وتؤدي عملية التحلل التي تعقب ذلك غلى توليد غاز الميثان، وهو غاز دفيئ يتسبب بإضرار للبيئة بما يفوق ثاني اكسيد الكربون بثمانين مرة.
وتعد عملية استخدام النفايات في عملية التصنيع هي حلا يتسم بكفاءة أعلى في إدارة النفايات بدلا من دفنها وحرقها، وهذا يعني أن صناعة الاسمنت هي مستهلك كبير للنفايات وتساهم بصورة أكثر في الاقتصاد الدوار (أي الانتاج والاستهلاك معا)
وهناك اربعة فوائد رئيسية لإستخدام النفايات في عملية التصنيع بالنسبة للعمل المناخي، ألا وهي
١
تخفيض التكاليف الاستثمارية العامة بشأن مرافق النفايات الجديدة
٢
تقليل مقدار العوادم والنفايات التي يتم القاءها في مدافن النفايات
٣
استخدام وقود بديل كإجراء يهدف إلى مواجهة التلوث.
٤
تقليل انبعاثات ثاني اكسيد الكربون في عمليات تصنيع الاسمنت لدينا
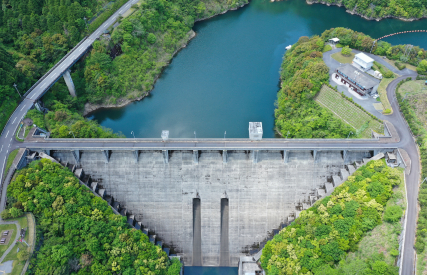
Clinker Factor Reduction
Clinker, the key component of cement, is produced by fusing together limestone, clay, and other materials in a rotary kiln at temperatures nearing 1500 Celsius. This is a very energy-intensive and carbon-emitting process. In fact, most direct CO2 emissions in the cement production process are generated by the chemical reaction of clinker production in our kilns. Our efforts concentrate on substituting it with byproducts from other industries like blast furnace slag, and fly ash. Waste from other industries and alternative raw materials allow us to reduce the clinker factor while maintaining the same quality and durability of our products. Our new clinker types have up to 20% lower CO2 emissions.
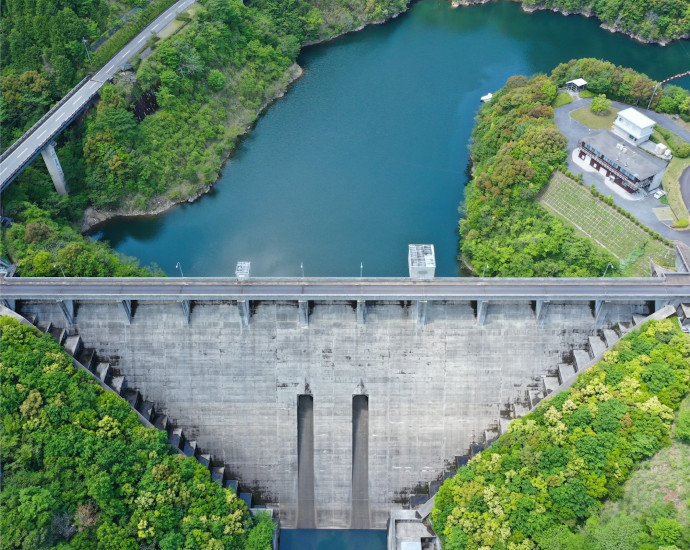
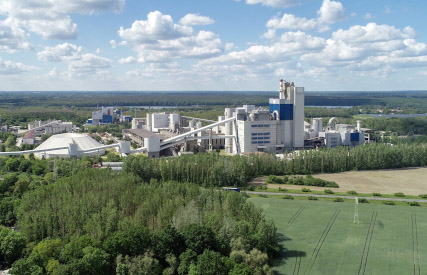
الطاقة المتجددة ومحدودة التكلفة
خلال عام ٢٠٢٠، حصلنا على حوالي ٣٠٪ من الطاقة المطلوبة لعملياتنا من مصادر طاقة نظيفة. ومن خلال هذا الاجراء، صارت الانبعاثات غير المباشرة لدينا والمرتبطة بالكهرباء المستهلكة في مصانعنا هي امر يساهم ايضا في تقليل البصمة الكربونية لدينا.

نتائج عام ٢٠٢٠
٩١٪
من مصانعنا المستهلكة للنفايات يقارب استهلاكها حوالي ٣ مليون طن من النفايات كوقود بديل.
+٣،٢٥%
من نسبة الوقود البديل العالمي لدينا
٢٩٪
من الكهرباء الخاصة بعمليات الاسمنت لدينا تأتي من مصادر طاقة نظيفة
-٢٣٪
من صافي انبعاثات ثاني اكسيد الكربون لكل طن من المنتح الاسمنتي، بما يمكننا من تجنب ٦،٨ مليون طن (من الانبعاثات).
إزالة الكربون من عمليات الانتاج لدينا
يعتبر برنامج "المستقبل يبدأ الان" هو برنامج طويل الاجل، حيث سيظل يعمل – في إطار عمليات الانتاج لدينا- على تقليل البصمة الكربونية لنا والوفاء بهدف ٢٠٥٠، ألا وهو إنتاج خرسانة خالية تماما من ثاني أكسيد الكربون دون غيرها.